Implementation of AI-based visual inspection equipment at Bosch manufacturing site in Japan
Contributing to the reduction of the workload for visual inspection
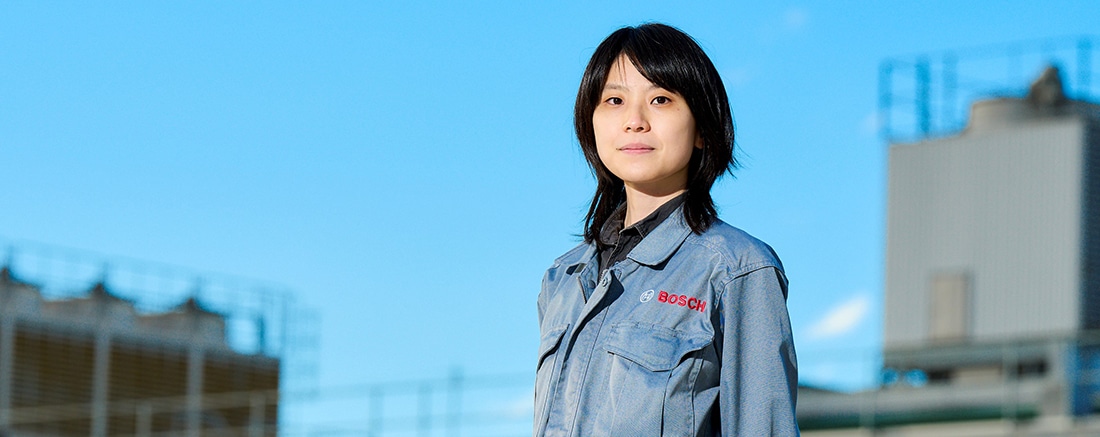
- Pick Up
- Power Solutions Division (PS)
- Production and Manufacturing Technology
- Monozukuri (Manufacturing)
- AI Implementation
Bosch manufactures a wide range of products for mobility, and actively incorporates the latest technologies such as AI in the manufacturing process. Specifically, what kind of technology is used and what effect does it have on the manufacturing site? Haruka Saito, who works in the Power Solutions Division at the historic Higashimatsuyama Plant and promoted the project to implement AI at the Yorii Plant, talks about these topics.
Power Solutions Division
Haruka Saito
[Video] Bosch engineers talk about the AI-based visual inspection automation project (Video: Japanese language)
*Please note that the audio will start when you press the play button.
If you would like to watch a video about Bosch's project to implement AI-powered equipment, please view the YouTube video above.
Implementing equipment that incorporates AI tools to reduce the burden of work at the site
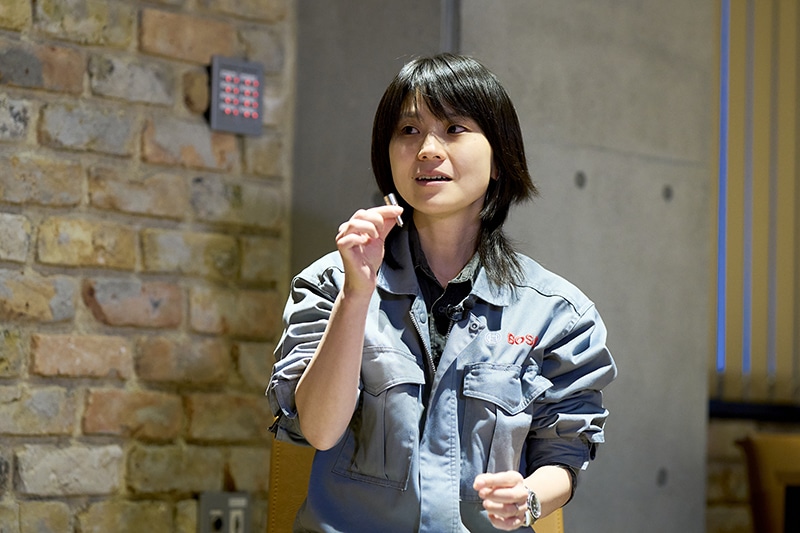
First, please give us an overview of the project that you worked on this time.
Saito: This time, I would like to introduce our project for automated visual inspection of the exterior of parts. Efforts to utilize AI in products and manufacturing processes are gaining momentum at Bosch locations around the world, and this new visual inspection system also incorporates an AI (deep learning) tool.

The product being inspected is a nozzle. An engine has a cylinder into which fuel is injected, and fuel comes out from the tip of the nozzle. Fuel comes out of a hole that is as thin as a hair.
Please tell us the details of the inspection.
Saito: A visual inspection device is used to inspect the shape and size of the nozzle hole, and the position of the opening, etc.
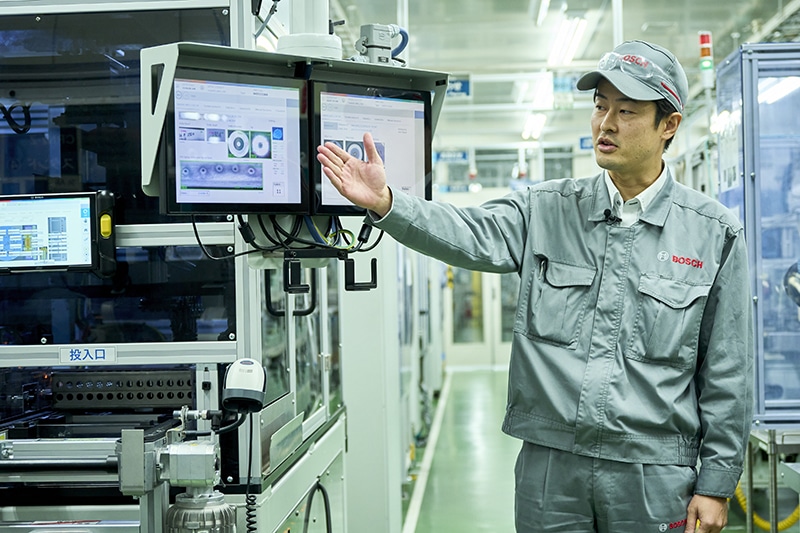
Originally, associates visually inspected all products on inspection tables. However we are gradually replacing the inspection with equipment, starting with the products that have large production volumes.
There are microscopes, but it is difficult to inspect the products one by one, in a limited time. In 2021, we began using visual inspection equipment at the Yorii Plant's manufacturing site.
Some people at the site have said that the burden on associates has been greatly reduced.
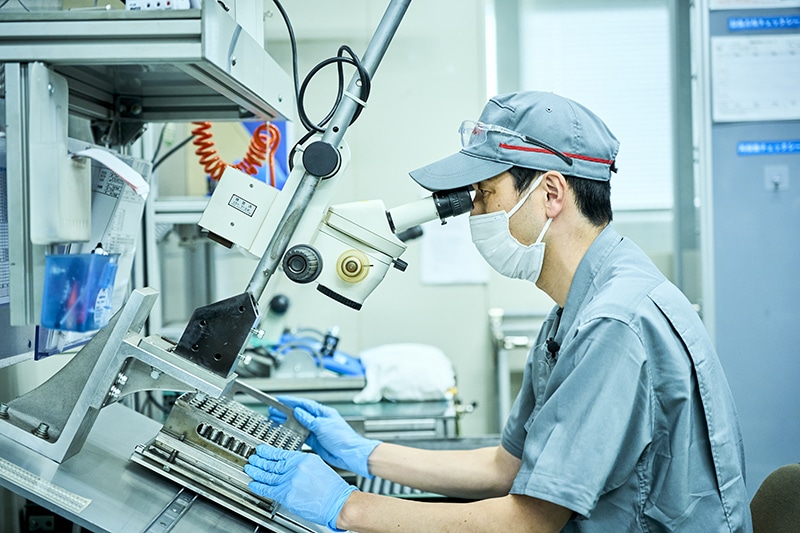
If inspections are done with equipment, the pace will be faster and the burden will be reduced.
Saito: Inspection work is a very nerve-wracking job, so it puts a lot of strain on the body. As a developer of machinery equipment, I would like to provide equipment that leads to improvements at production sites. If this equipment can contribute to the improvement of on-site work, I think it is good that we are working with it.
It seems that the equipment currently is being used to inspect one of the products. Are there any plans to expand its usage in the future?
Saito: Yes, we are currently developing it so that it also can be used for other products as well. In addition, the equipment is being used to inspect the exterior of the nozzle, but the interior is being inspected by associates. We would like to develop it so that the equipment can also inspect the interior.
The introduction of deep learning improves development speed and judgment accuracy
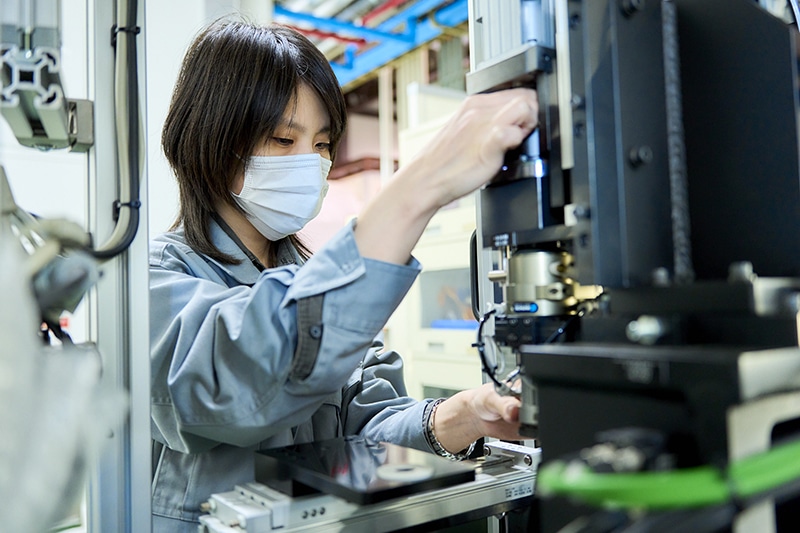
Please tell us about the image processing that is used in this project.
Saito: The technologies used for image processing can be broadly divided into conventional rule-based methods and AI (deep learning), which is a relatively new technology. With rule-based technology, it can be difficult to detect things if they are not clear or distinct, like color differences.
However, it does not mean that deep learning is superior in all cases. The items that will be inspected should be taken into consideration, and it is necessary to decide whether the technology to be used is rule-based or if deep learning can also be used. In the case of this project, the use of deep learning resulted in increased development speed and judgment accuracy.
Why can deep learning do things that rule-based could not determine?
Saito: Rule-based takes what is called a feature value (such as the area, length, and size of a shape), and sets a threshold for it. On the other hand, in the case of deep learning, the concept is that it automatically extracts feature values and sets thresholds. So, feature values that were difficult for people to get through rule-based, are expected also to be picked up and used for judgment.
Success is possible through on-site visits to build relationships of trust and organizational cooperation
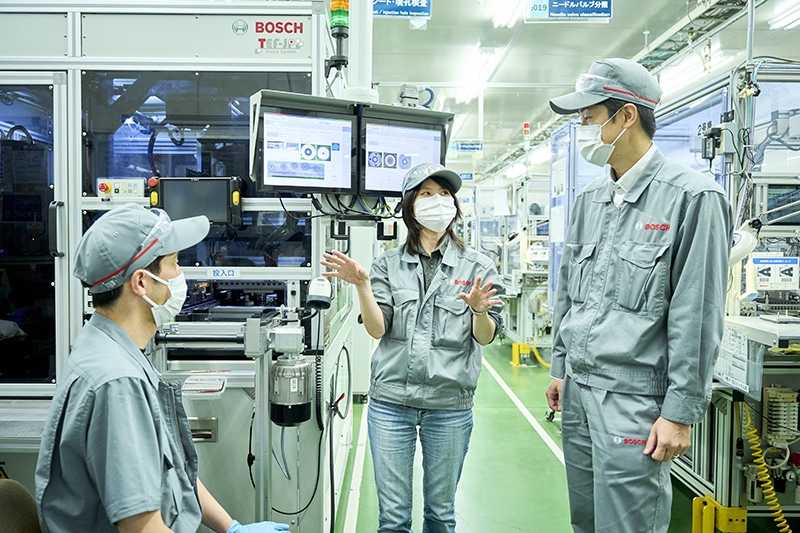
What made this project so successful?
Saito: One of the factors is that the use of AI has made it possible to achieve things that were previously impossible, such as speeding up development.
In addition, as the project progressed, the understanding of the members increased, and I think a reason for success was that we were able to gain organizational cooperation. It went well because it was understood that image processing technology has some difficult aspects, and the on-site team cooperated to devise ways for the parts that were difficult for the equipment to handle. On the other hand, from the perspective of cost reduction, we need to work even harder to achieve some more results.
Through this project, is there something that you learned that is necessary to succeed as an organization?
Saito: I usually work at the Higashimatsuyama Plant, but the delivery destination was the Yorii Plant. So, after developing the equipment to a certain level, the equipment was moved to Yorii. I went to Yorii every day for about three months in order to proceed with the local start-up.
By doing so, I think I was able to communicate with the associates in the field and build a relationship of trust. By visiting the site, I was able to see the actual product right away, so I learned that it is important to look closely at the site and the actual product and know it well.
As in this case, at Bosch is there frequent communication with overseas locations?
Saito: It depends on the department you belong to and the nature of your work, but I think you will have opportunities to a varying degree to have contact with overseas locations and see English texts.
There is a worldwide group of engineers in the Power Solutions Division who perform image processing and non-destructive inspection. In my case, I belong to that group and participate in monthly information exchange meetings.
Among those exchanges, there was an introduction about what one location was doing. We felt that the technology could also be used here, which led to this project.
By collaborating globally, do you often come into contact with and learn things that you would not be able to know in Japan alone?
Saito: You can learn about good products from overseas and learn good methods. For example, at an overseas location, when planning a new project there are times when a target is set to say, "If this goal is not achieved at this point, we will withdraw." That target is called a stop criterion, and I think that method is very good when proceeding with new things.
Rather than making a big investment and then failing, it is better to fail while the damage is small. And then start something new again. I think it is better to do that, and I think it is important to obtain such methods from overseas.
AI is a tool. We would like to use it if it can achieve the goal.
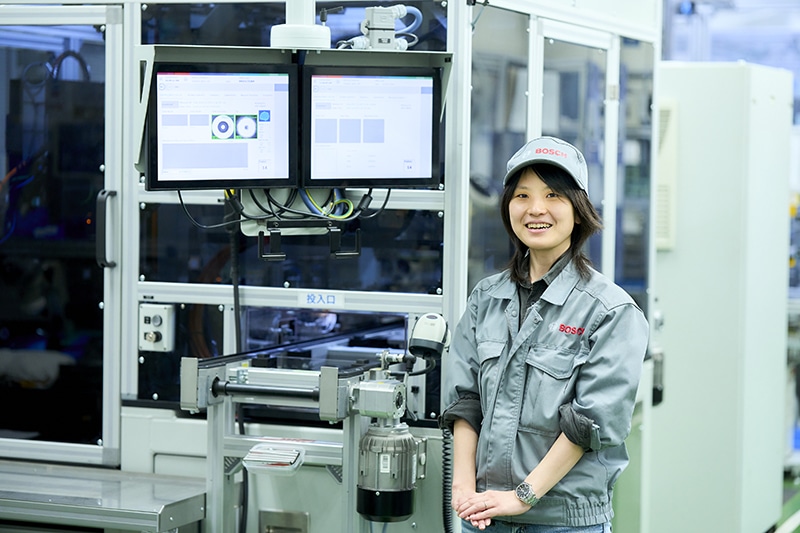
I think this project has become one of the success stories. Is AI still attracting attention within Bosch?
Saito: Certainly, it was a breakthrough in the field of image processing, but I think AI is a tool or a means. This time, AI was used because the goal was to reduce costs and improve workability, and AI happened to be able to contribute to that goal. However, if the goal can be achieved in a different way, I think that is fine.
Just because it is a new technology, it does not mean that you should avoid it, and on the other hand it does not mean that you should jump on unnecessarily. I think a good stance is to utilize it if you can.
At Bosch, there are moves to actively utilize AI, such as the establishment of AI-related departments overseas. If these efforts can be used successfully in our development, we would like to actively use it in the future.
Thank you. Finally, do you have a message you would like to convey to readers about Bosch and this project?
Saito: This time, I was the one who talked about the project, but there are many people who have cooperated in the project, including those who are actually working at the Yorii Plant, and there are various other projects being carried out at Bosch in addition to this project.
Many associates work in various fields such as manufacturing, sales, development, quality assurance, and production control. As a result, the company has increased sales and can make a profit. I think this should never be forgotten.
Even work that is usually done as a matter of course is the result of the efforts of the members and the accumulation of know-how, so I hope that the spotlight will be on that as well.
I believe that this project is also a great asset for Bosch, and I found that success stories have been created through organizational collaboration.
If you are interested in Bosch after reading this article, please watch the video.
Click here for the video (Japanese language)
* This page is a reprint of the contents of "Talentbook".
Source: https://www.talent-book.jp/bosch/knowhows/51220