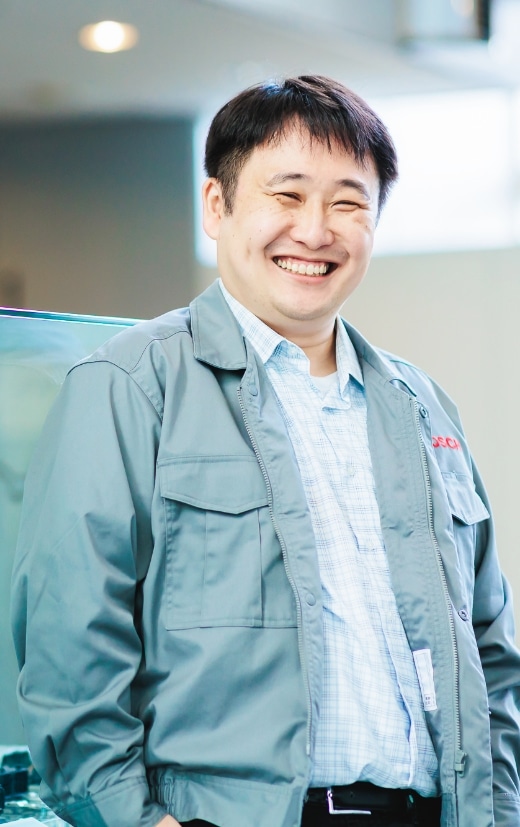
POWER SOLUTIONS
DIVISION
Yuichi B.
ECU Systems Office, ECU Project Group 3
SW Engineer
Joined Bosch in 2014
From a semiconductor manufacturer where utilized experience in a research lab, to taking on new challenges in the long-admired automotive industry
In the ECU Project, I am in charge of SW development of a unit (ECU) that electronically controls the powertrain that transmits the power of the vehicle's internal combustion engine to the tires. Our major mission is to collaborate with engineers in Japan and overseas to drive forward the project and achieve the type of movement and performance required by automobile manufacturers.
I have loved cars since I was a child, so much so that I went on a trip around Japan in my first car, which I got from one of my senior classmates when I was a student. After graduating, I joined a semiconductor manufacturer where I could utilize my experience in a research lab for electronic data, but I still had passion and enthusiasm to make automobiles. The semiconductors I was in charge of were shipped to a wide range of manufacturers and were used in a variety of products. In particular, products for automobiles were required to have high quality that could function in both hot and cold environments. I decided to change jobs to the automobile industry because I wanted to see with my own eyes how the products I had worked on were actually being used.
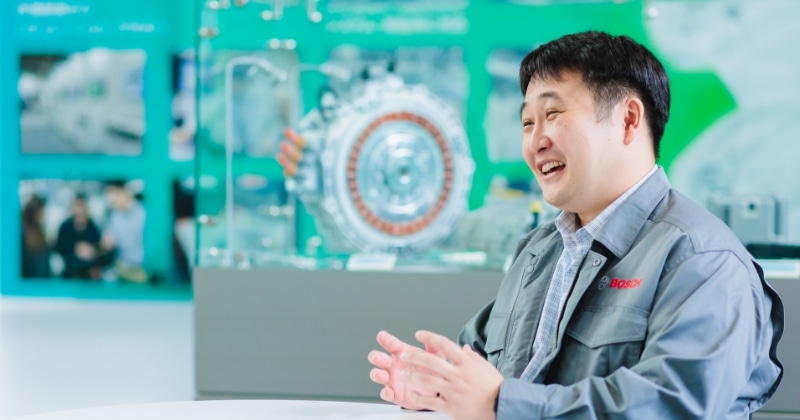
Together with global development members, ECU development that meets customer requirements
In the SW development project for ECUs, we respond to requests from our customers, who are domestic automakers, while communicating with overseas members in India, Brazil, Vietnam, Germany, and other countries. In order for the project to progress, it is important to fill a role between the customer and the development team members so that there are no discrepancies in perception during the development process. For example, to avoid misunderstandings such as "the customer's request is not conveyed" or "Bosch development members cannot convey their concerns or difficulties". This is an important role.

The proportion varies depending on the project, but sometimes 30-40 members are involved in Japan, in addition to 30-40 members overseas. At first, I was worried about my English ability, and whether I would be able to communicate with so many members. However, the only person who cared about such things was me, who is Japanese. Overseas members are accustomed to interacting with Japanese people, so they speak slowly and rephrase things into simple words. I changed my mind and now I think that "Bosch is the perfect environment to experience using English for business for the first time."
Before joining Bosch, I had imagined it to be a dry and meritocratic foreign-affiliated company. However, in reality, even members who joined the company mid-career can learn the SW development process and how to proceed with work. In addition, there is not only on-the-job training, but also in-person training. This overturned my previous image and now I feel that "Bosch is a company that supports associates so much." In my case, the knowledge of semiconductor peripheral circuits that I gained in my previous job is still useful, but I can also acquire the necessary specialized knowledge after joining Bosch. I feel that what is more important is to look in the same direction as our customers and build a relationship of trust.
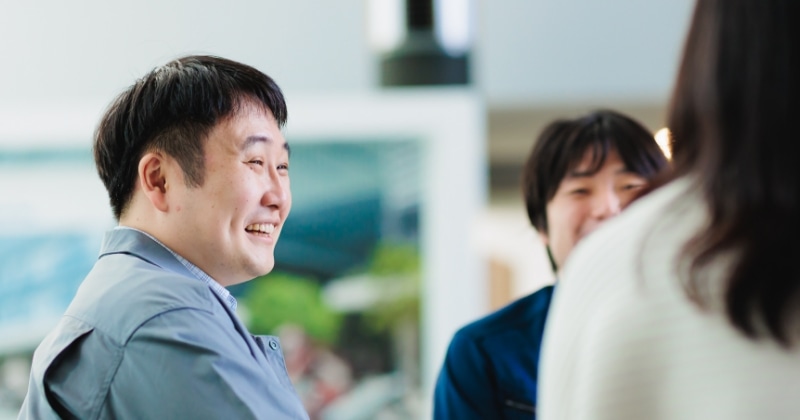
Strengths of a diverse organization that customers and team members can rely on
Currently, when we receive inquiries from overseas members, such as "We are envisioning this kind of development, but we don't know what the customer will think," we approach the person in charge and make inquiries in advance. I feel that I have become a facilitator so that the project will proceed smoothly. The basis is a relationship of trust that allows us to consult personally with the person in charge on a daily basis. We have received permission to freely enter and exit the customer's office building and test site, and we are able to exchange technical opinions in front of the actual vehicle.
In order to introduce a new generation of ECUs, I was assigned overseas for one year at the German headquarters, which handles advanced technology. Not only was I able to learn about the new engine ECU up close, but I was also able to meet directly with overseas members with whom I usually communicate online, so I feel that I am able to communicate with them at a higher quality even after returning to Japan.
Our strength is that we have development members globally, and we can provide solutions to a single problem from various values and perspectives. I think one of the interesting things about Bosch is that we are able to learn that interpretations differ depending on the country, technology, and manufacturer.
I like my job working with internal combustion engines. In gasoline vehicles, if the balance between air, fuel, and ignition is lost, the engine might stop and fuel efficiency will deteriorate. It is interesting and enjoyable to make a fuel-efficient car through performing difficult and precise fine adjustments, and I think it is also fun to drive. On the other hand, our customers continue to take on the challenge of new technologies, such as electric drives and EVs, and I would like to keep pace and continue to gain new knowledge at Bosch.
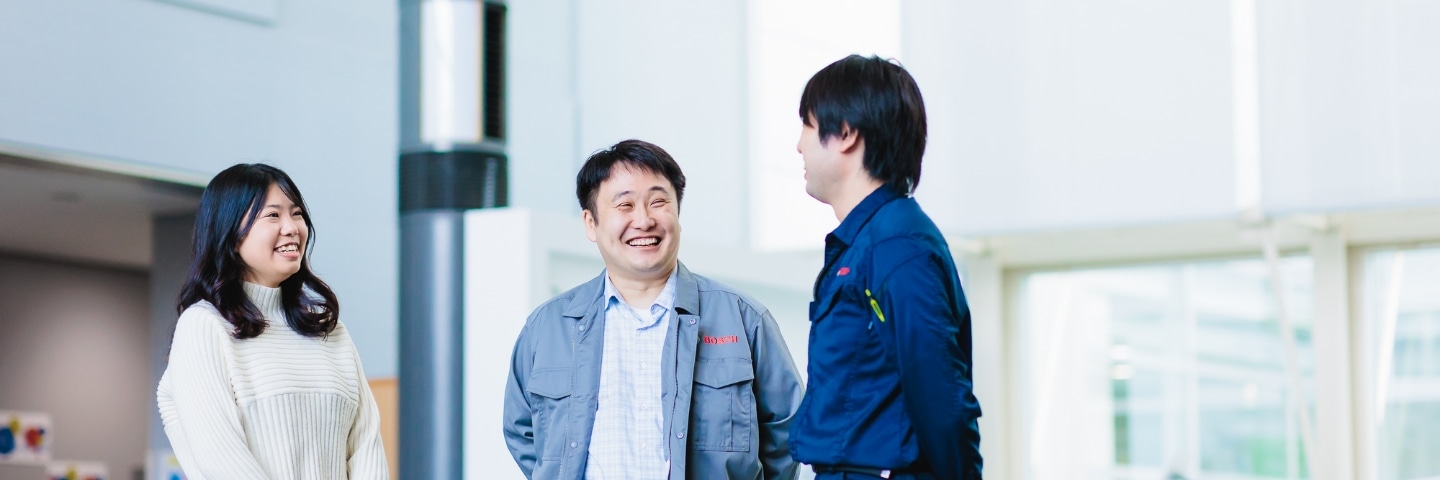