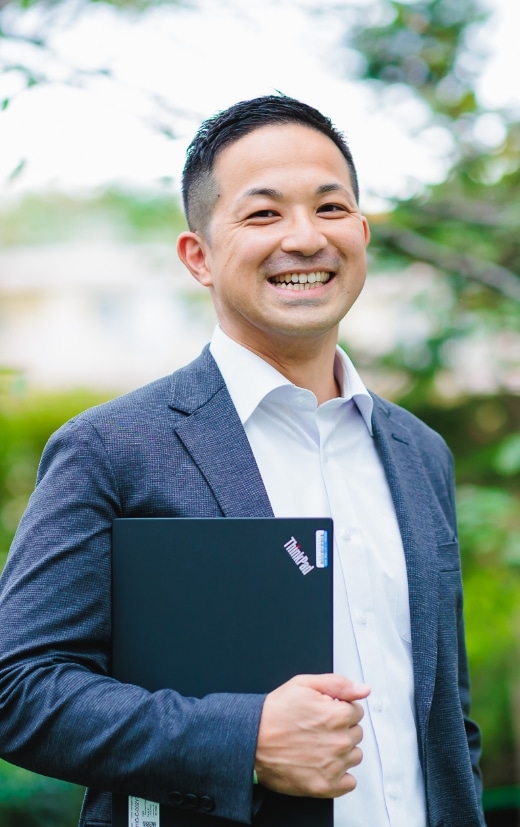
VEHICLE MOTION
DIVISION
Shunsuke S.
Vehicle Motion Division
Test Management Engineer, Engineering
Joined Bosch in 2021
Desire to create better products through a flatter relationship with overseas bases
At university and graduate school, I was engaged in research on mechanical systems. As a new graduate, I joined a Japanese auto parts manufacturer with a high ratio of overseas sales in hopes of working on a global scale. There, I was in charge of system design for mass production development of steering controller units, and also participated in a global project that I had wanted. I also spent one year at a development base in France as a technical support representative for overseas development and production bases.
My previous job was in a global environment that fulfilled my wishes, and I was able to experience the joy and difficulty of working with people from completely different cultures than in Japan. However, my previous company was a Japanese company, and the head office is only in Japan. I came to think that I would like to try manufacturing with a flatter relationship with overseas bases. After working for about 10 years, I started looking for a new job, mainly at foreign-affiliated companies, in order to change the environment and take on challenges.
Among those I was considering, I chose Bosch because of its wide range of business fields and its environment where I could take on challenges with people from different cultural backgrounds. Through the selection process, I felt that the people and the atmosphere at Bosch were the most attractive. In addition, Bosch is promoting Smart Work as a unique activity, and the working environment, such as remote work and the ease of taking paid leave, is also attractive.
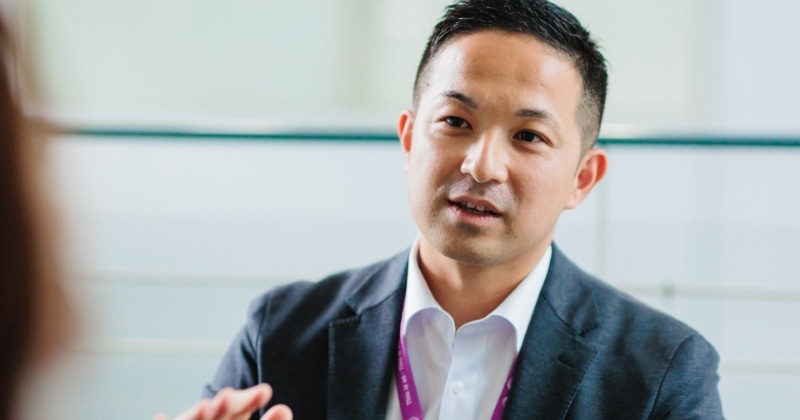
Involving members in six countries and supervising overall testing for mass production
Currently, I am a test manager in a mass production development project for steering products for Japanese automobile manufacturers. I am in charge of customer contact for evaluation and verification, as well as overseeing all aspects of testing. The mission of the test manager is to monitor whether the test plan is optimal across the entire system, software, mechanics, and hardware, and to actively follow up and resolve any progress delays or problems.

The projects I am involved in are large-scale projects involving many bases such as Japan, Germany, China, the United States, India, and Vietnam. We communicate flatly with engineers at each site. Troubles are inevitable in a development project, but you can demonstrate your skills as a test manager in how to solve problems and proceed smoothly with each global base. In addition to technical knowledge, the ability to involve and coordinate with many members is required. I think that this is a high-level mission, but I feel that it is unique to Bosch to be able to act independently and with a great deal of discretion while experiencing cutting-edge technology in the automotive industry.
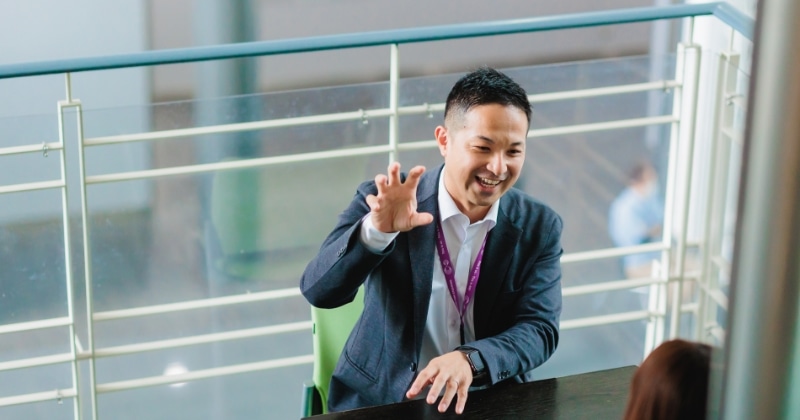
Overcoming differences in speed and processes, and aiming to become a project manager
I originally applied to Bosch with the aim to become a system project leader, but I thought that it would be better first to gain experience in the products and the working style at Bosch, and I was offered the position of test manager.
When I actually joined Bosch, I was surprised to find that although the basic knowledge in development did not change, there were differences in the way of thinking and work processes between Bosch and Japanese companies. What I particularly struggled with was the sense of speed. At Bosch, if there is rationality and grounds for something, decisions can be made quickly, even if they are challenging. The speed was quite different from my previous job, so it was difficult to break away from the culture I was used to. Therefore, I used talks with my superiors and the mentor system, which allowed me to consult with managers of other divisions, to get accustomed to my work while voicing my concerns and resolving them. On the other hand, even though Germany is the headquarter, the presence of Japanese bases is high, and the fact that Japan's business is respected is a gap in a good sense.
I feel that my experience at Bosch, which is completely different from my previous environment, will be a great source of inspiration for my career. First, I learned Bosch's methodology as a test manager, and the next step is to become a system project leader, as I have hoped for. Going forward, as a project manager, I would like to lead a mass production development project to success.
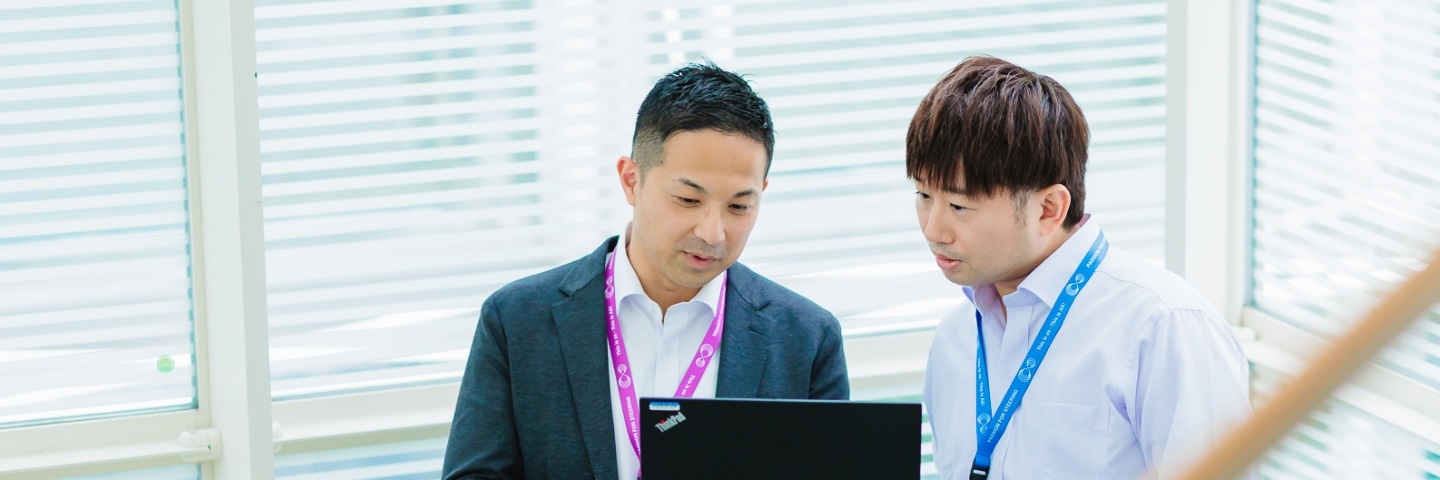