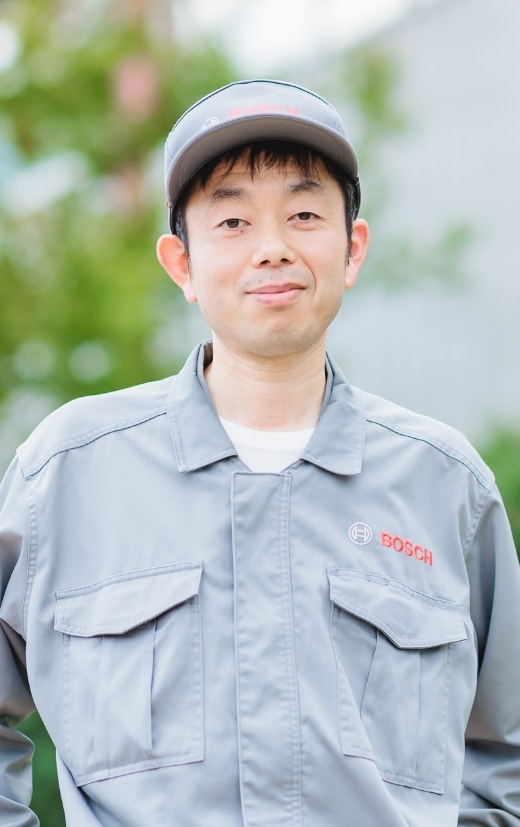
VEHICLE MOTION
DIVISION
Toshihiro N.
Tochigi Plant Manufacturing Control, Manufacturing Department
Sensor Assembly Section
Manager
Joined Bosch in 2016
- Vehicle Motion Division (VM)
- Production and Manufacturing Technology
- Monozukuri (Manufacturing)
- Sensors
Eagerness to experience a higher level of work at a world-leading company
After graduating from graduate school, I was in charge of production technology for parts processing at a supplier that develops engine parts. There are two reasons why I thought about changing jobs. One reason was that I wanted to stay in Japan but work in a global environment. The other reason was that I wanted to challenge myself by being involved in not only processing, but also the production and manufacturing technology of the assembly process. I wanted to broaden my skills, so I started looking for a new job.
I had been involved in the automotive industry, so I had known about Bosch for a long time. I decided to join Bosch, the world's leading automotive parts manufacturer, because I thought that I would be able to work in a global environment while staying in Japan, and also grow by experiencing a higher level of work.
After joining Bosch, I was entrusted with manufacturing technology for assembly lines for hydraulic unit parts. My wish before joining Bosch was to challenge myself by becoming involved in the assembly process, and my wish came true. I also feel that I have acquired leadership, communication skills, and problem-solving skills to achieve goals by involving those around me. Now, in my seventh year at Bosch, I am in charge of the sensor assembly section. In addition to further improving the productivity of the products for which I am responsible, I am now in a position to promote the creation of a workplace where it is easy for anyone to speak up and make proposals.
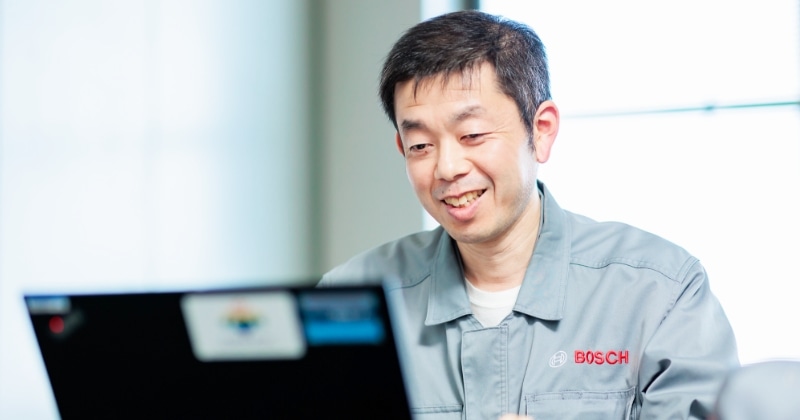
Involving members and contributing significantly to improving factory performance
After joining Bosch, I became very aware of leadership during my first project. At that time, I was working alone on improving the production line, but it was not going well. When my boss saw this, he advised me, "You don't have to work alone. Get others involved and take the lead." I was able to change my behavior significantly.
Instead of trying to solve the problem alone, I talked to members of the maintenance group and the on-site staff involved in the production line and asked them, "Would you like to work together?" Even though I had just joined Bosch, the members around me listened to my opinions and promptly shared a variety of information. From small actions to results, the work became more interesting, and the number of participating members increased day by day.

Before I knew it, a "kaizen" (continuous improvement) activity team was formed, and I took the lead. As a result of steadily working on improvement activities, the Tochigi Plant became the number one performer among the plants in charge of the parts. In addition, the results have boosted the morale of the participating members, and positive changes have been brought forth, such as members themselves preparing "kaizen" proposals, planning review meetings, and exchanging requests.
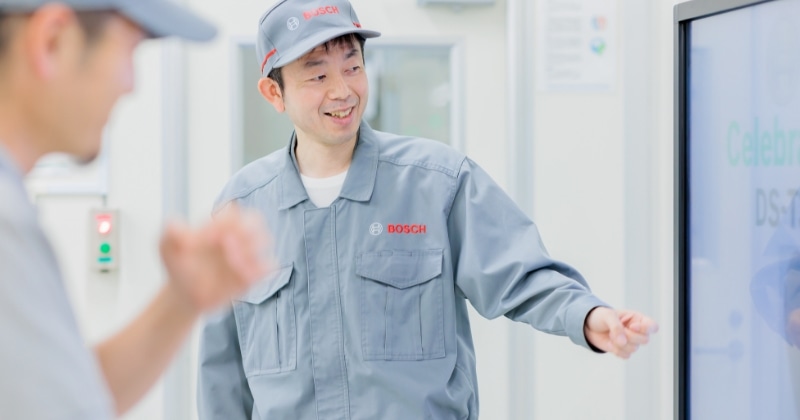
Concentrate on essential "kaizen" (continuous improvement) work and take on the challenge of global business while staying in Japan
Everyone can speak freely, make proposals, and act as a leader. I believe that Bosch's culture was a factor in the success of the aforementioned initiatives. Bosch has a unique culture of listening to everyone, regardless of their position or year of employment, and many employees are conscious of actively communicating. This was a boost to promote the "kaizen" (continuous improvement) activities.
My wish was also fulfilled to work in a global environment while staying in Japan. Although the Tochigi Plant has many Japanese associates, it holds regular meetings with production bases around the world, including Germany, China, and India. I was entrusted with leading meetings conducted in English, and I think that not only my communication skills but also my language skills improved.
In addition, Bosch is active in capital investment. Bosch has a culture of "investing in what you need", which allows us to focus on the essential work of improving the workplace. Bosch is also a very rewarding workplace for engineers in the production engineering field.
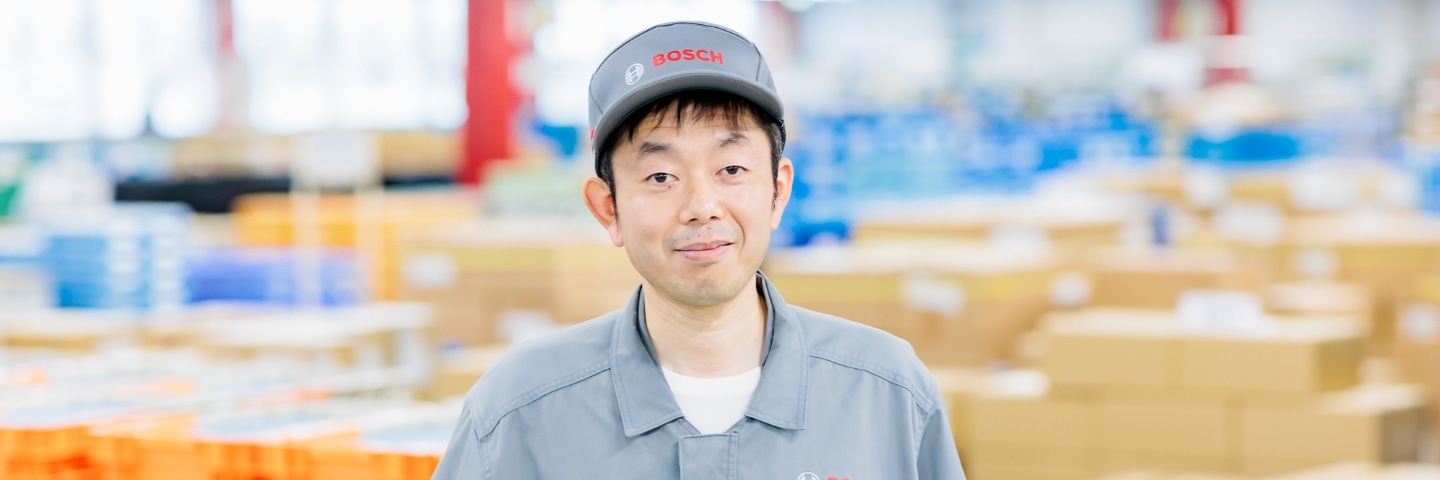