目視による検視作業の工数削減に貢献、日本の工場へAI外観検査装置を導入
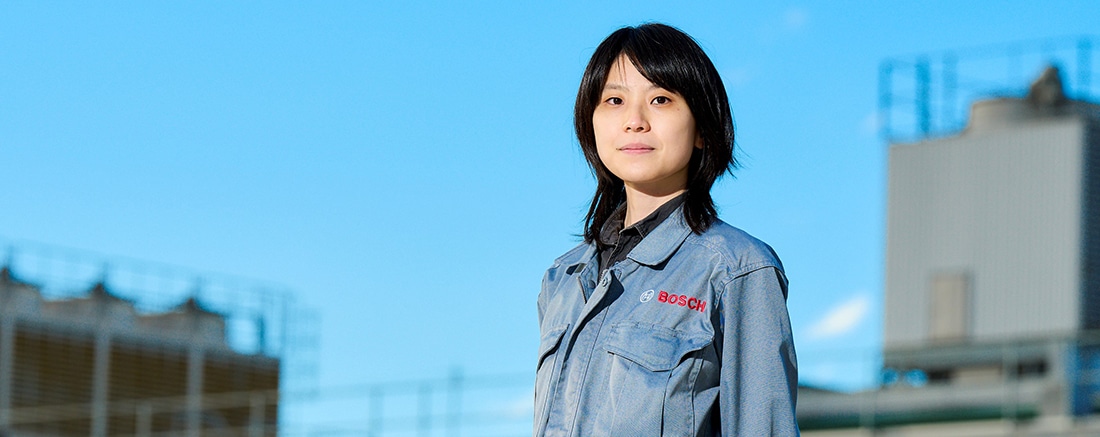
モビリティにおいて、幅広い製品群を製造しているボッシュ。製造工程ではAIをはじめとする最新技術を積極的に取り入れています。具体的にどのような技術を用いて、製造現場にどんな効果をもたらしているのでしょうか。歴史ある東松山工場に勤務し、寄居工場へのAI導入プロジェクトを推進したパワーソリューション事業部の齊藤が語ります。
パワーソリューション事業部
齊藤 遼
【動画公開中】エンジニアが語る、AIを活用した外観検査自動化プロジェクトの歩み
※再生ボタンを押すと音が出ますのでご注意ください。
ボッシュのAIを活用した機械導入プロジェクトについて動画で観たい方は、ぜひYouTubeでご覧ください。
AIツールを取り入れた装置を導入し、現場の負担を減らす
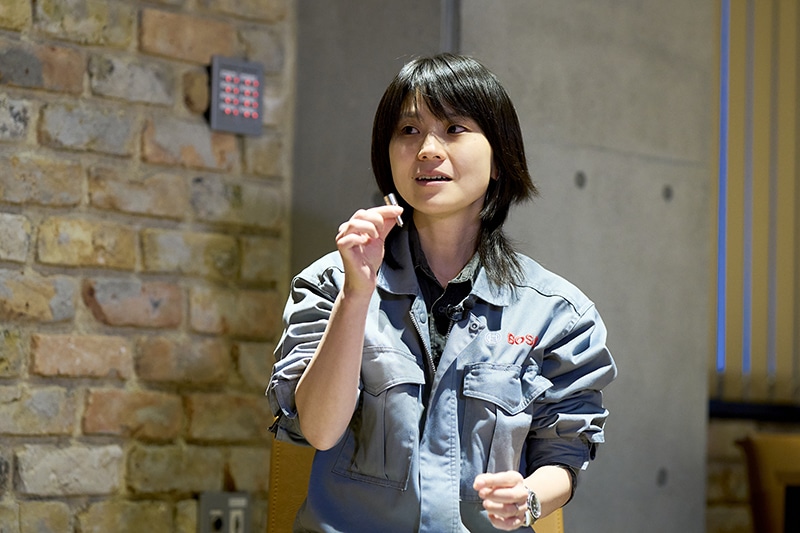
まず、今回取り組んだプロジェクトの概要について教えてください。
齊藤:今回ご紹介するのは、外観検査の自動化プロジェクトです。世界中のボッシュのなかで製品や製造工程にAIを活用する取り組みが昨今盛んになってきており、今回の外観検査装置もAI(ディープラーニング)ツールを取り入れています。

検査している製品は、ノズルです。エンジンにはシリンダーがあり、その中に燃料を噴射するのですが、その燃料はノズルの先から出てきます。髪の毛くらいの細さの穴から、燃料が出てくる形です。
具体的な検査内容を教えてください。
齊藤:ノズルの穴の形状や大きさ、開いている位置などを外観検査装置で検査していきます。
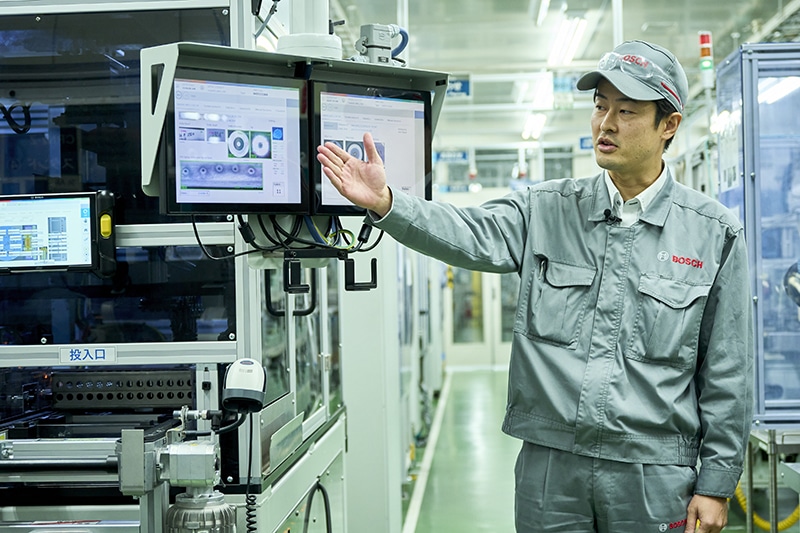
もともとは全品番を人が検査台で目視により検査していたのですが、生産量の多い品番から段階的に機械に置き換えています。
顕微鏡はありますが、限られた時間の中で1個ずつ検視するのは大変な作業です。2021年から寄居工場の製造現場で外観検査装置の運用が始まっています。
現場からは、作業者の負担が非常に低減したという声も上がっています。
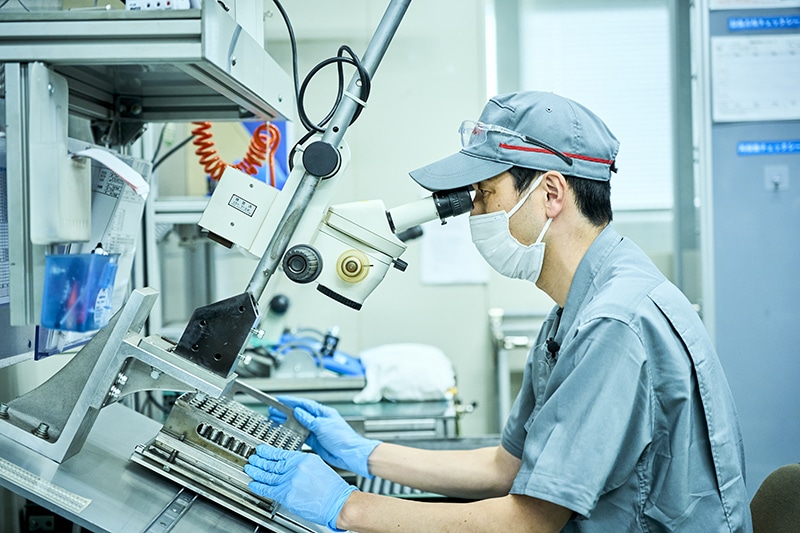
やはり機械で検査を行うと、ペースも早くなり負担も軽減するのですね。
齊藤:検視作業は非常に神経を使う仕事なので、身体への負担も大きいです。機械設備を開発する側としては、生産現場の改善につながるような設備を提供できればと思っています。今回の設備も現場の作業改善に貢献できていれば、私たちとしても取り組んで良かったと思います。
現在機械では1つの品番を検視しているそうですが、今後拡大予定はあるのでしょうか?
齊藤:はい、他の品番もカバーできるように現在開発を進めています。また、今はノズルの外側を機械で見ていますが、内側は人が見ている状態なので、内側の検視もできるよう開発をしていきたいと考えています。
ディープラーニングの導入により、開発スピードも判定精度も向上
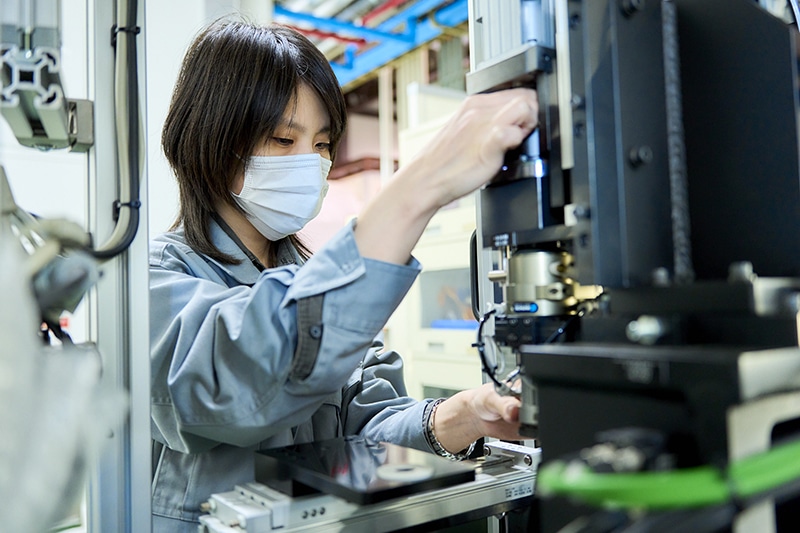
─今回のプロジェクトで導入された画像処理について教えてください。
齊藤:画像処理に用いる技術には、大まかに分けると、従来からある手法のルールベースと、比較的新しい技術であるAI(ディープラーニング)があります。ルールベースの技術だと、色の違いみたいなものが明確にないと検出が難しい場合があるんです。
ただ、どんな場合でもディープラーニングが優れているということでもなくて。活用する技術は検査項目を鑑みて、ルールベースにするかディープラーニングも活用するのか判断が必要になります。今回のプロジェクトの場合、結果的にディープラーニングを使うことで、開発スピードも判定精度も上がりました。
ルールベースで判別できなかったことを、なぜディープラーニングではできるのでしょうか。
齊藤:ルールベースでは、図形の面積や長さ、大きさといった特徴量と呼ばれるものを取得して、それに対して閾値を設定します。一方ディープラーニングの場合は特徴量の抽出も閾値の設定も自動で行ってくれるようなイメージです。人がルールベースで取得するのが難しかった特徴量も抽出し判定に使用しているはずです。
現場に足を運んで信頼関係を築き、組織的な協力体制があってこその成功
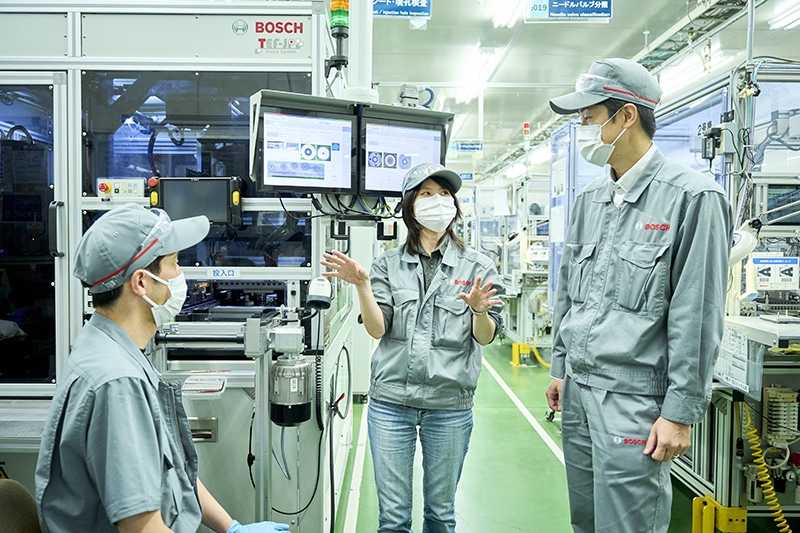
今回のプロジェクトが成功した要因を教えてください。
齊藤:ひとつの要因としては、AIを活用したことで開発スピードが速まるなど、今までできなかったことが実現できるようになったことです。
また、プロジェクトを進めていくうちにメンバーの理解も浸透してきて、組織的な協力体制が得られたことも成功した理由だと思います。画像処理技術は難しい部分もあると理解してもらえたほか、装置側で対応が難しい部分について現場側で工夫するよう協力してもらったからこそ上手くいきました。一方でコスト削減効果の観点では、もう少し成果が出せるように、さらに頑張らなければいけないところです。
今回のプロジェクトを通して、組織として成功するために必要だと学んだことはありますか?
齊藤:私は普段東松山の工場で働いていますが、納入先が寄居工場だったので、ある程度のレベルまで開発したあとは装置を寄居に移設しました。現地での立ち上げを進める上で、3カ月ほど毎日寄居に通いました。
そうすることで現場の方々とコミュニケーションが取れて、信頼関係を築けたと思います。足を運ぶことで現物もすぐに見られたので、現場や現物をよく見てよく知るのは大切だと学びました。
今回の事例もそうですが、ボッシュでは、海外とのやり取りも頻繁に行われているのでしょうか?
齊藤:所属している部署や仕事内容にもよりますが、多かれ少なかれ海外と接点を持ったり英語の文章を見たりする機会はあると思います。
私の場合、パワーソリューション事業部内に画像処理や非破壊検査等を行う世界的な技術者集団がありまして、そこに所属し月例の情報交換会に参加しています。
その中で「うちの拠点ではこういうことをやっている」という紹介があり、「その技術はこちらでも使えそうだ」と感じて今回のプロジェクトにつながった形でした。
グローバルで連携することで、日本だけではわからないことに触れたり学んだりすることは多いのでしょうか。
齊藤:海外のいい製品を知れたり、いい方法を学んだりすることができます。たとえば海外では、新しくプロジェクトの計画を立てるときに、“この時点でこの目標が達成できていなければ撤退する”というターゲットを設定する場合があります。そのターゲットのことはストップクライテリアと呼ばれていますが、新しい物事を進めるときにその手法はすごくいいなと。
大きく投資してから失敗するよりも、傷が小さいうちに失敗しておく。そして、新しいことをまた始める。そうした方がいいと思いますし、こういった手法を海外から得られることは重要だと思います。
AIはあくまでも手段。目的を達成できるのであれば使っていきたい
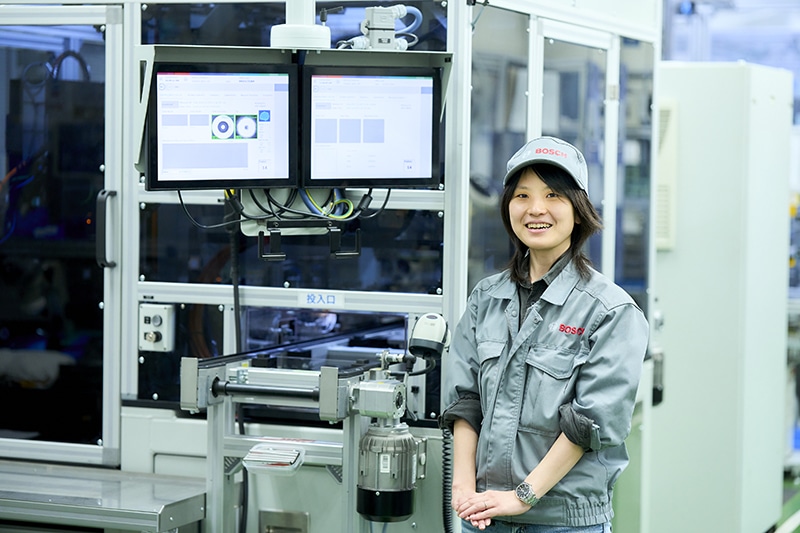
今回のプロジェクトは成功事例のひとつになったと思いますが、ボッシュ内でもやはりAIは注目されているのでしょうか?
齊藤:確かに画像処理の界隈ではひとつのブレイクスルーではあったと思いますが、AIはあくまでも手段だと私は思っています。今回であればコスト削減と作業性の改善という目的があり、たまたまAIがそれに貢献できそうだったので使いましたが、もし違うやり方で達成できるのであればそれでもいいと思います。
新しい技術だからといって避けるのも違うし、かといってむやみに飛びつくのも違うので、活用できるのであれば使う、というスタンスがいいのではないかと思っています。
実際に海外でAI関連の部署が立ち上がるなど、ボッシュでは積極的にAIを活用しようという動きがあります。その取り組みが私たちの開発に上手く使えるのであれば、今後も積極的に活用していきたいです。
ありがとうございます。最後に、今回のプロジェクトやボッシュという会社について、読者のみなさまに伝えたいメッセージはありますか?
齊藤:今回は私がお話をさせていただきましたが、実際に寄居工場で作業している方をはじめ協力してもらった方はたくさんいますし、このプロジェクト以外にもボッシュではいろいろな仕事が行われています。
製造、営業、開発、品質保証、生産管理など、本当にたくさんの従業員がさまざまな仕事をして、その結果、会社の売上が立って利益が出ている。それを忘れてはいけないと思っています。
普段当たり前のように行われている仕事も、担当している方の努力があり、ノウハウが積み重なった結果、成果が出ているので、そちらにもスポットが当たるようになるといいなと思います。
今回のプロジェクトもボッシュにとって大きな財産になっていると思いますし、組織の連携によって成功事例が生み出されていることがわかりました。
今回のお話を聞いてボッシュに興味をお持ちの方は、ぜひ動画もご覧ください。
▶動画はこちら
※このページは「talentbook」に掲載された内容を転載しています。
出典:https://www.talent-book.jp/bosch/knowhows/51220