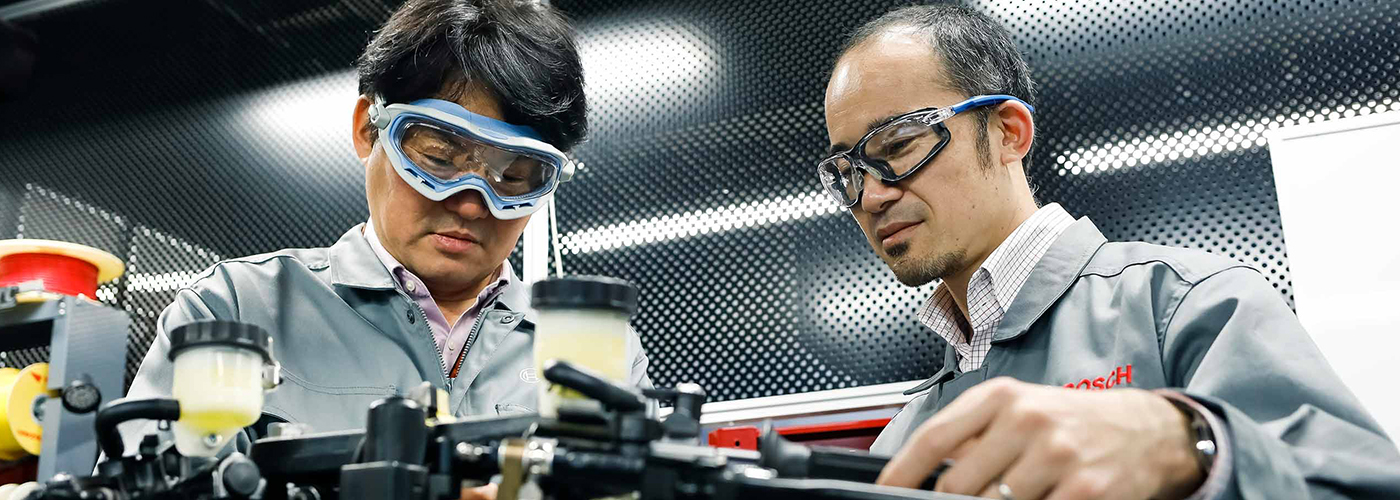
-
大髙 順
JUN OHTAKAモーターサイクル&パワースポーツ事業部 開発
1997年入社 -
小川 貴士
TAKASHI OGAWAモーターサイクル&パワースポーツ事業部 開発
2008年入社
ポケットサイズのABSをつくろう
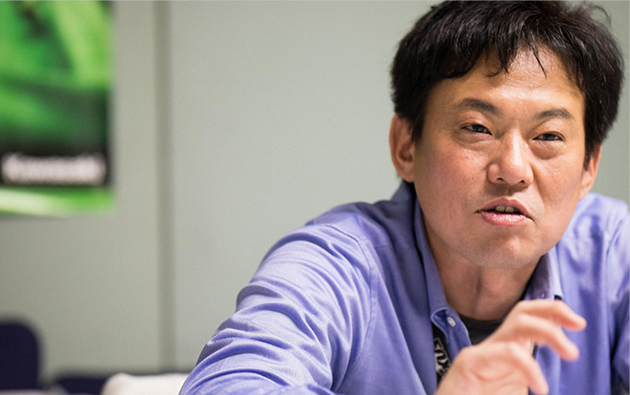
2000年初頭、バイクに搭載されるABSには自動車向けのものが代用されていた。
しかし、もともと自動車向けにつくられているため、その大きさや重さが原因となり、バイクに搭載できないことがほとんどだった。
さらに、ライダーの間でABSは重くて場所をとり、楽しいライディングを邪魔するものというイメージだけが先行してしまい、バイクにおけるABSの普及率は世界中で非常に低いものだった。
また、バイク事故での死傷者数は増加の一途をたどる深刻な状態が続いていた。
この状況を解決するには、ABSの小型化・軽量化、コストパフォーマンスの向上が不可欠であり、国内外のバイクメーカー各社をはじめ多くの人々がその実現を待ち望んでいた。
当時、自動車向けABS開発に携わっていた大髙。
バイクメーカー各社から現状のモーターサイクル用ABSに対する要望を聞いたとき、自分たちの手でなんとかしなければという使命感でいっぱいだったという。
「しかし、これまでボッシュではABSの基本設計を行っていたのはドイツ。日本はそれをもとにアプリケーション開発をすることが主だったので、自分たちだけでコンセプトを立てて、基本設計から行っていくという経験がほとんどありませんでした。そのため、なかなかアイデアが思い浮かばず、悶々とした日々を過ごしていました」。
そんなある日、大髙の上司の一言が突破口となる。
「上司はおもむろにポケットからタバコを取り出して、“このサイズのABSをつくろう”と言い出したのです。当時のABSはタバコの箱の倍以上の大きさがあり、正直、最初はとても驚いたのを覚えています。そのサイズにするためには、何が問題で、どんな技術が必要か、1つ1つ逆算して考えていきました。そう、すべてはあの一言からはじまったのです」。
2006年、大髙たちは世界最小モーターサイクル用ABS(ABS9)の実現に向けて、一歩を踏み出した。
立ちはだかる多くの壁
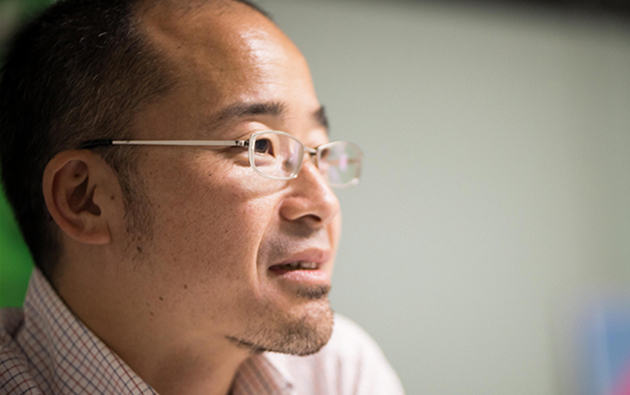
ライダーの命を守りたいという多くの社会的なニーズがあり、それに対するアイデアや技術的なコンセプトがあっても、慈善事業ではないので当然利益を生み出さなければならない。
プロジェクトの本格始動を目前にして、大髙たちの前には多くの壁が立ちはだかっていた。「私たちが思い描いていたバイクに特化した世界最小のABSを実現するために、設備投資のほかにさまざまな壁を越える必要がありました。
たとえば電子設計と機構設計の壁をはじめ、事業部間の壁やソフトウェアとハードウェアの壁など、私たちが今、思いついたからといって、すぐにつくれるものではなかったのです。
また、製造を担当するボッシュジャパンの工場においてもドイツから展開された工程でつくることに慣れてしまっており、新たな製造工程開発というものが受け入れられにくい状況でした」。
しかし2008年、事態は一気に進展する。大髙たちの提案を親身になって聞いてくれていた、当時の執行役員とドイツ人のプロジェクトリーダーのふたりが中心となり関係各所を説得。
そのおかげで社内の承認もとれ、モーターサイクル用ABS9の開発にGOサインが出されたのだ。
それからは、電子制御式ブレーキシステムの機構設計エキスパートが必要だという話になり、即戦力として小川に白羽の矢が立った。
「当時は他社に在籍していましたが、新たなものを開発しようと動き出している環境で自分も挑戦したいと思い、ボッシュへの転職を決意。入社してすぐにモーターサイクル用ABS9のプロトタイプを見せられたときは正直オモチャかと思いました。従来のものの半分以下の大きさだったので、メンバーの本気をひしひしと感じたのを覚えています」。
小川も加わり、プロジェクトチームは総勢5名に。
足かけ2年を要したが、プロジェクトはついに本格的にスタートを切ったのだ。
想定されるリスクを徹底的に払拭
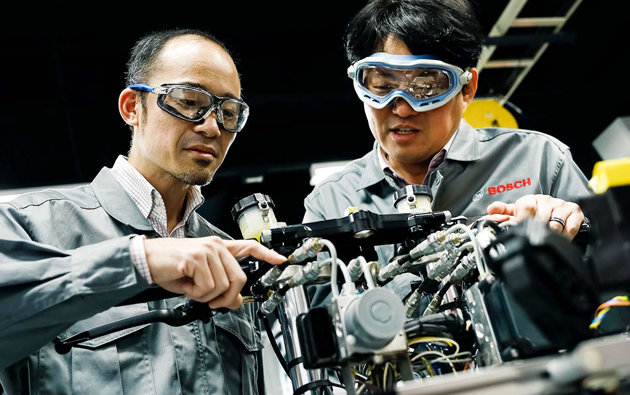
大髙と小川はまず、各関係部署やサプライヤーと連携を密にしながら、すべてをパラレルで進行。
手探りの中、1つ1つ挑戦を重ねていった。たとえばドイツから展開された製造ラインに慣れてしまっている国内工場で、自分たちが書いた設計図をもとに製品をつくるには、どのような工程が必要なのか。
それを検討・調整していくことは、プロジェクトチームにとって大きなチャレンジだった。
途中、想定外のハプニングもたくさん起きたが、プロジェクトチームにはある共通認識があった。
それは、量産後に不具合を1つも出さないということだ。
もし量産が決まった後に問題が生じてしまったら、このようなチャンスはもう二度と訪れないかもしれない。
だからこそ、世の中では想定できないくらいのレベルまでテストを繰り返し行った。
バイクならではの搭載環境を想定した高い振動条件での試験や温度・湿度耐久試験、さらに不燃性はもちろん、浸水などによる二次故障に至るまで徹底的な検証を実施。
また、テスト車両に開発中のABSを搭載し、システム開発・実車適合開発担当のエンジニアに実車で試してもらってフィードバックを受けるなど、徹底的に評価を行った。
ほかにも部品の質を追求し、部品によってはμmレベルでの部品製作、小川が担当していた樹脂系部品に対しては何度もつくり直しを行い、高い精度を要求していった。
「サプライヤーの工場がベトナムにあった関係で、量産開始直前まで日本とベトナムを行き来していました。これも、私たちが求める寸法を出すためでした」と小川は振り返る。
試行錯誤の末、2009年にモーターサイクル用ABS9の量産が開始。
小型化と軽量化を実現したABS9は瞬く間に国内外問わず、多くのバイクメーカーで採用され、ABSに対するエンドユーザーの認識も変化していった。
そして何より量産開始後から何年もの年月が経ったが、未だにモーターサイクル用ABS9の設計不良による不具合返却は1台もない。
その事実が、プロジェクトチームが追い求めてきた完成度の高さを物語っている。
超えるべきハードルは過去の自分たち
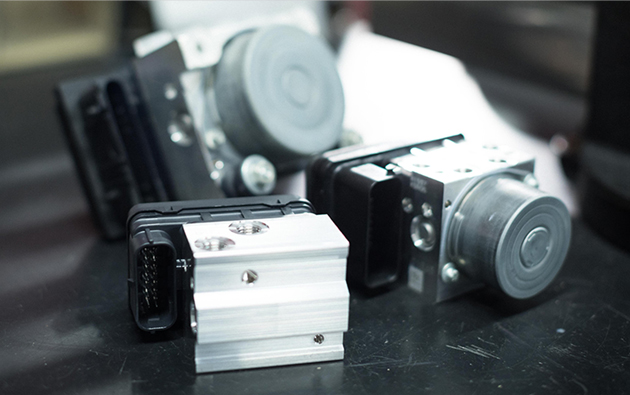
ただABS9の搭載実績は、エンジン排気量の大きい大型バイクに多いのが事実。
また近年、世界的にモーターサイクル用ABSの装備を義務付ける国が増えつつあり、欧州や日本などの地域のみならず、小型バイクの人気が高い新興成長市場でのABS装備義務化も予定されている。
たとえばインドでは2018年4月以降、排気量125cc以上のすべての新型バイクにABSの装着が義務化される予定である。
そのような背景から、2012年に次世代小型モーターサイクル用ABS10の開発がスタートした。
「どうすれば小型化と軽量化を実現できるかというコンセプトを考え、試作品をつくってはテストベンチ上で試験を繰り返していました。しかし、これがなかなかうまくいきませんでした」。
小川がそのように言うのも当然で、モーターサイクル用ABS9ではすでに大幅な小型化と軽量化を実現しており、さらなるサイズダウンはかなり高いハードルだったのだ。
「デザインは成り立っているのに、製造の観点から見ると構造に無理があることもしばしば。実際に工場に行っては、みんなで何時間も熱い議論を交わしていました」。
意見がぶつかることもあるが、大髙はそのようなときにこそいいアイデアが出るのだという。
「誰かが議論をしていると特に、自分はこうだと思っていても担当分野ではないことには口を挟みにくいもの。でも、そこを笑われる覚悟で発言すると一瞬、場がやわらぎ、いいアイデアが出たりするのです」。
その繰り返しが、プロジェクトを少しずつ前に進めていく。
ABS9からのいちばんの変更点はABSユニット外部に装着されていたモーターを外から見えないユニット内部に配置したこと。
モーターサイクル用ABS10を排気量の小さい小型バイク向けに限定し、さまざまな部品を小さくすることで小型化と軽量化の両方を実現した。
数々のプロセスを経て、2016年にようやくABS10の量産化が決定。
すでに世界中のバイクメーカーへの採用が予定されており、今後この次世代ABS10が搭載されたバイクが世界中の道を走ることだろう。
その日を迎える頃にはきっと、大髙と小川の次なる挑戦ははじまっている。
※掲載社員の仕事内容・部署は
取材当時のものです