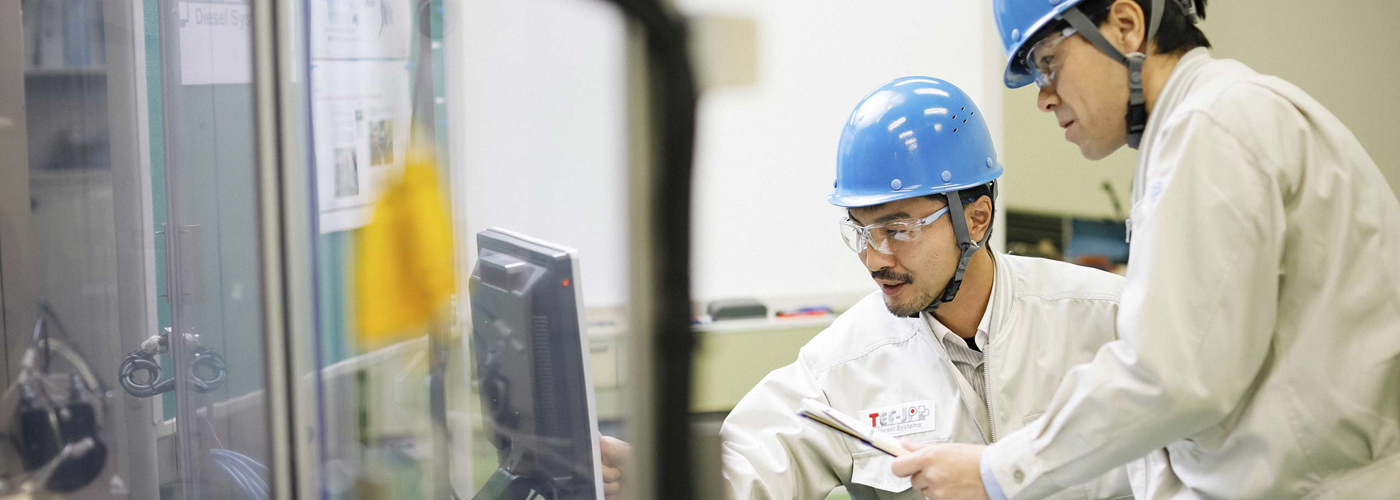
-
山田 貴史
TAKAFUMI YAMADAパワーソリューション事業部 製造部門生産技術
1982年入社 -
柴﨑 淳平
JUNPEI SHIBASAKIパワーソリューション事業部 製造部門生産技術
2007年入社 -
杉田 真
MAKOTO SUGITAパワーソリューション事業部 製造部門生産技術
1992年入社
コモンレールシステム登場による変革
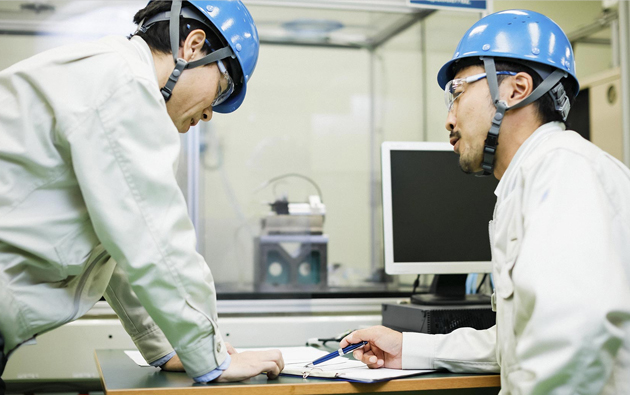
1990年代初頭、日本のディーゼルエンジン市場は逆風にさらされていた。
ディーゼルエンジン搭載の大型車で特に古く、何らかの故障をかかえている車両は黒煙を撒き散らしながら走行しており、大気汚染の原因の1つとして問題視されていたのだ。
1995年から排ガス規制の基準値が一気に引き上げられ、その後の東京都で制定された条例がさらなる追い討ちをかけた。
東京都は国が定める以上の厳しい数値を設定し、それに満たないディーゼル車の都内の走行を禁止したのだ。
長年、ディーゼルシステムの生産設備機械設計に従事していた山田は、この規制には驚きを隠せなかったという。
「私たちは1985年頃からディーゼルシステムの高性能化のため、燃料噴射のキーであるインジェクターノズルの内面を研削するスピンドルの開発・評価を繰り返し、生産性と形状精度を高めるとともに法規に対応してきました。しかし、このときの排ガス規制に対応するには従来の技術の延長では難しく、ディーゼルエンジン自体が大きく変わる必要がありました」。
そこで登場したのが、ボッシュが世界に先駆けて開発した乗用車用コモンレールシステムである。
コモンレールシステムとはエンジン燃焼室内に燃料を吹き込む際、高圧ポンプを使用し燃料に2000バール(海底2万メートルと同じ圧力)の圧力をかけレール(パイプ)に蓄圧し、インジェクターから各シリンダーに最適な量と最適なタイミングで多段噴射する最新燃料噴射システムのこと。
これは燃料に使用する軽油は揮発性が低いため、圧力が高い状況で燃料が噴射されるとシリンダー内部で霧状に拡散されかつ、燃料が微細になるため燃焼効率が向上し、粒子化合物(PM)の発生を抑えることができるのだ。
ただコモンレールシステムでは燃料を高圧化するため、従来のインジェクターノズルは使用できなくなり、材料や工法を変更しなくてはならない。
特に大きな変更点は、それまでは熱処理前にドリルで開けていたノズルの噴射孔を、内面加工後に開けるようになったことだ。
「噴射孔を開ける工程がいちばん最後になり、ノズルの穴が開いていない状態で内面を研削しなければなりませんでした。ノズルの先からクーラント(切削油)を入れることができないため、私たちは切削油を出しながら加工する、オイルスルーの機能機構を盛り込んだスピンドルを開発しました」。
しかし、まだまだ改善の余地はあり、いかに内面の形状を正確に研削し、作成していくかというのが今後の課題として残っていた。
日本のモノ造りに対する自負
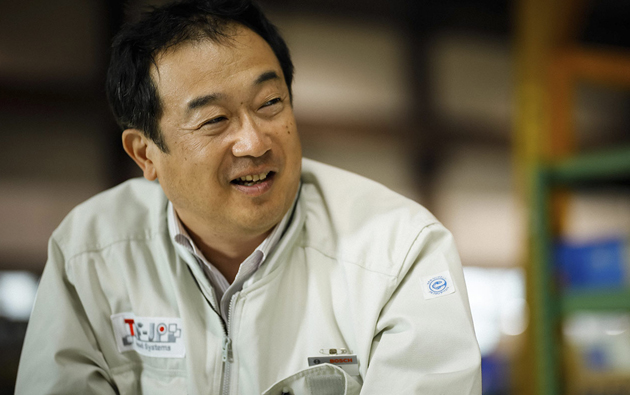
理論上、スピンドルの1分間の回転数を上げれば加工時間を短縮でき、形状精度も高められるはずだった。
しかし、はじめは何度トライしても回転数はなかなか上がらなかった。
また速いだけでなく低振動でスピンドルを回さなければならないため、回転精度の分野で高い技術を持つ日本のサプライヤーから高精度セラミックベアリングを採用するなど試行錯誤の日々が続いた。
「私たちメンバーの頭を悩ませたのは、回転数の安定性。瞬間的にはある程度の回転数が出せたのですが、製造工程を想定した長時間の連続運用テストをすると耐久性に問題が発生し、年単位で使い続けられるものではありませんでした」と杉田は当時を振り返る。
そのような状況が続いていたが、誰もあきらめようとしなかったのは、日本発のモノ造り技術を世界に広げたいという強い意志があったからだ。
「ボッシュの基本スタンスとして、たとえばラインに敷設する生産設備においてもドイツで開発したものを標準とし、ワールドワイドの各拠点に展開するという方式をとっています。ですが、工機・保全を担当する私たちは加工機をはじめ、組立機や評価装置をすべて自分たちでイチからつくり、製造ラインに入れてきました。現在、このような枠組みの中で自分たちの立ち位置を模索していますが、モノ造りに関しては日本がいちばんという自負があります。だからこそ、それをスピンドルで証明したかったのです」。
山田はまっすぐ前を見てそう語った。
柴﨑が入社した2007年、プロジェクトに1つの転機が訪れる。日本にドイツ本社から社員が訪れ、試作品のスピンドルを見て絶賛。
ドイツに帰国した後、日本でつくられたスピンドルのことを報告してくれたのだ。
そしてその後、ドイツ側から回転数を少し抑えた実用的なものをつくってほしいという要望が入った。
日本発の世界標準技術の実現に、一歩近づいた出来事だった。それから実用化を目指して、1分間に数十万回転とオイルスルーを両立させたハイスピードスピンドルを開発。
2010年には、日本ですべてを開発・設計・製造したスピンドル搭載の加工機ができあがるほど、順調に評価と改善を繰り返していった。
この頃から柴﨑がメンバーに本加入し、プロジェクトはさらに前進していくのだが、ここに至るまでにはこんな逸話がある。
2008年の年明け、入社から1年が経とうとしていた柴﨑がちょうど機械づくりのプロセスから機械修理の実習が終わり、本格的に機械設計エンジニアとして歩きはじめようとしていた頃だった。
山田は定期面談の場で「将来、どのような仕事をしてみたい?」と柴﨑に問いかけた。
すると柴﨑は「機械としておもしろそうなのは加工機、特に内面研削盤の仕事に携わるエンジニアになりたいです」と答えたのだ。
その柴﨑の想いを汲み取った山田は「日本の内面研削技術をボッシュワールドワイドに展開したいから、柴﨑さん、背中にそれを背負って、まずはドイツに行商に行ってもらおうかな」と提案したところ、「ぜひ、やらせてください」と柴﨑は力強く返答したのだった。
工機保全を担当する山田のグループにとって、伝統的なプロジェクトを加速させる可能性を秘めたエンジニアのひよこが誕生した瞬間である。
日本発のスピンドル、ドイツに導入
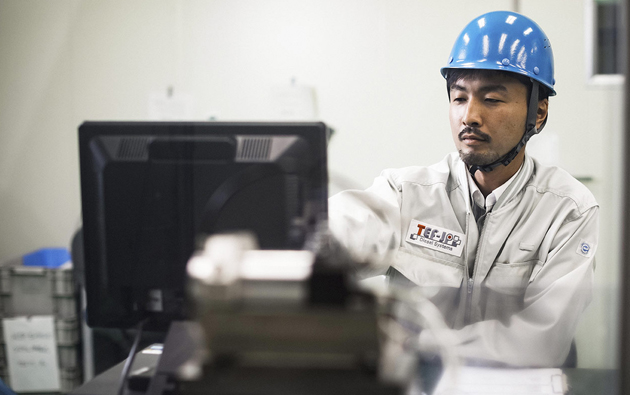
2012年、ドイツ本社でついにスピンドルのコンペが実施された。
競合の中にはスピンドルの製作実績を豊富に持つメーカーが含まれていたが、日本発のスピンドルが無事採用されることになった。
その勝因は、製品だけではなく実際の評価データをあわせて提案したからだった。
山田は「工法開発や製造を担当する部署と密に連携していることはもちろん、自分たちでつくった製品を評価するフィールドがすぐ隣にあるということが私たちの何よりの強みです」と語る。
コンペ後は、実際にドイツの製造ラインにハイスピードスピンドルを導入し、3ヵ月24時間フル稼働で評価試験を行うことになった。
日本とドイツの加工機の仕様が違うため、スピンドルをドイツの加工機に搭載できるよう柴﨑が適合開発・設計を行った以外は、何事もなく評価は終了した。
そして晴れてドイツへ導入されることになった日本発のスピンドル。スピンドル制御装置の設計を担当した杉田はこう振り返る。
「みんなが一生懸命つくったスピンドルを最初に持っていくのは責任重大でした。でも日本でテストを繰り返し行い、絶対の自信を持っていたので、スピンドルそのものに対する心配はありませんでした」。
事実、杉田がインストールした1号機は約4年が経った今も、性能を維持したまま、24時間フル稼働で壊れずに活躍し続けている。
しかし、ハイスピードスピンドルの製造にはかなりの精度・工期を要するため、大量生産を試みようとすると品質にバラツキが出るという問題があった。
「グローバルスタンダードになったときに、QCDをいかに安定させられるかが私のタスクでした」と語るのは柴﨑。
「もともとトライアル品だったので、量産向けにルールを設けていませんでした。
また部署内には、スピンドルは生産が完了してもテストベンチで試験運転を行い、評価をクリアしてはじめて出荷されることから量産は厳しいのではという意見もあり、まずはチームの意思統一を図ることからはじめました」。
そのような柴﨑を山田と杉田がサポートし、現場の製造責任者や担当者に掛け合っては、日本発のハイスピードスピンドルを世界の標準技術にするという大きなビジョンを共有していった。
少しずつ、でも着実に、現場は1つになりはじめていた。
量産後のハプニングを超えて
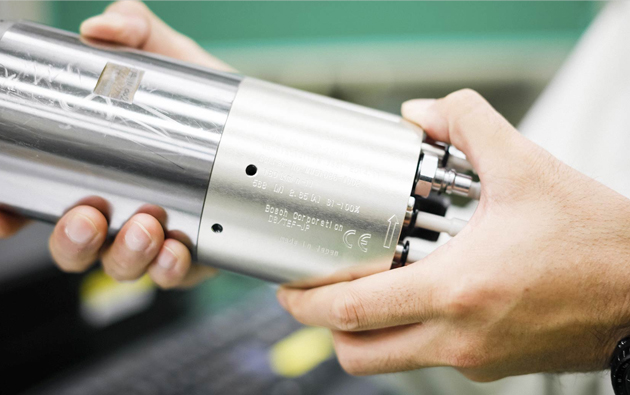
もっとも想定外だったことがある。
量産段階に入ったにもかかわらず、ドイツで立て続けにハイスピードスピンドルが壊れたときだ。
さすがにこのときは、山田をはじめメンバー全員が青ざめたという。
「幸いだったのは、最初に杉田がインストールしたスピンドルは壊れずに動き続けていたこと。杉田本人によりインストールされたものは問題なく稼働しており、ドイツの担当者がインストールしたものだけが壊れていたのです。約4年間フル稼働しているという実例があったから、ドイツから壊れた旨の連絡は来ても、我々のスピンドルが悪いと言われたことはありませんでした」。
ただ、と柴﨑は続ける。
「フル稼働しなくてはならないスピンドルが止まってしまっていたので、ドイツ側の生産計画に狂いが出てしまっていました。
私たちは一刻も早く復旧させる必要があり、予備のスピンドルを送りながら、原因を調査し、対策案を導き出していきました」。
今回の件を踏まえて、マニュアル作成の話が今、進んでいると柴﨑は言う。
「スピンドルを導入する方法、取り回しの方法やクーラントサプライヤーの選定に至るまですべてを日本サイドで決めようと思っています。今は納入先としてドイツがメインになっていますが、近く、フランス、トルコ、ブラジルをはじめ、ワールドワイドに広がります。だからこそ、このスピンドルの扱い方のワールドワイドスタンダードを決めるために、現在週1回ドイツとやりとりをしています」。
今後も継続してスピンドルのクオリティーを安定させていくことがプロジェクトチームの当面の目標になっている。
しかし、日本の技術力の真価を世界中に証明する日は、きっとそう遠くはないはずだ。
※掲載社員の仕事内容・部署は
取材当時のものです